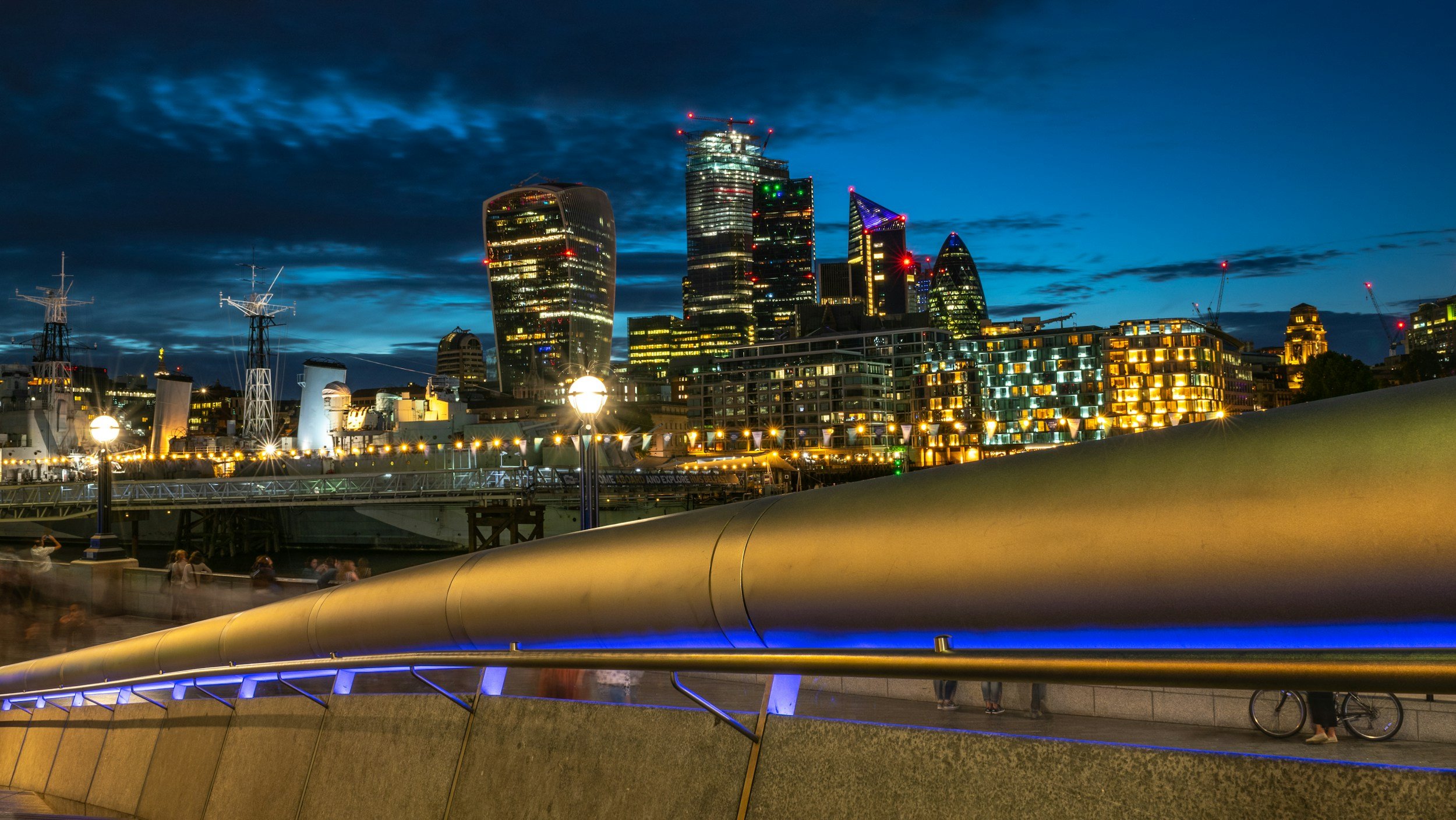
Dynamic Leadership. Unparalleled Quality.
Delivering excellence for our clients in every project.
At Evans Industrial Inc., we look at every client project as a true partnership. We understand the immense value our clients bring to our society, and take pride and ownership in every opportunity to collaborate in creating meaningful work.
Our revolutionary engineering, progressive leadership, expert team and dedication to quality is how we continuously deliver exceptional results for our clients.
We are also committed to providing cost-effective solutions for our clients and formulating efficient construction methods to deliver projects ahead of schedule whenever possible.
FEATURED PROJECTS
Power Generation Facility - Steam Valve Replacement
Evans Industrial was contracted by a Power Generation Facility to replace 7 Main Stream Valves. Our dynamic team of skilled workers used innovative construction solutions to overcome technical obstacles which resulted in significant cost reduction and project length for our client.
Power Generation Facility
Replaced 7 Main Steam Valves in two weeks working two shifts
Valve body material: ASTM A217
Piping material: ASTM P91, Inlet 16” Schedule 160, Outlet 12” Schedule 160
100% Weld Acceptance
The unique location of the valves in the unit posed a logistical challenge for workers to access and would typically require a 250 ton crane. Commissioning this equipment would be the easiest solution, but would add significant cost to the project.
Leveraging our team’s ingenuity, we delivered a cost-effective solution by designing and installing temporary monorails above the valve. This provided direct rigging access to the valves without the added expense of a crane and resulted in significant cost savings for our client.
Our team was also able to cut weld inspection time of the project. The 9-chrome material used required a 14 hour stress relief cycle. Understanding this delay within the project scope, our expert welders and quality control personnel created a more efficient process to complete the project. Rather than waiting between heat cycles to perform the varied tasks, our team worked within the heat cycles which enabled the completion of both welding and stress relief in conjunction. This process allowed immediate inspections of welds, all passing 100% X-Ray acceptance, saving 12 hours per weld on project time.
Combined-Cycle Power Plant - Hot Gas Piping Replacement
When a leading Water and Power Generation facility contracted Evans Industrial to replace their hot gas piping, we implemented comprehensive project management and productive scheduling to deliver project results with safety, quality and efficiency.
Combined-Cycle Power Plant
• Replaced hot gas path stainless steel piping in 4 units
• 90 welds, 316 stainless steel sizes 8” to 4”
• Install stainless steel tubing for instrumentation 1,000 linear feet
• Passivation of stainless steel field welded components
• 10% X-Ray, 100% Acceptance
• Submitted R1 form and quality control package following
completion of the project.
The project required simultaneous replacement of hot gas piping in four turbines. Leveraging a thorough planning process, we created an effective working schedule for each of the four turbines independent of one another.
Utilizing Primavera P6, we developed a robust, detailed schedule load of man-hours dedicated to each task. We reviewed this scheduling track every 24 hours to identify recourse potential roadblocks and optimize the acceleration of the project.
Our scheduling management further increased productivity for the project by allowing us to share resources among the units. We assembled four crews of highly skilled workers who were able to safely remove the existing piping and install new piping with proficiency. Each crew featured dedicated quality control personnel to ensure impressive service standards were met during construction. All welds were passed 100% X-Ray acceptance.